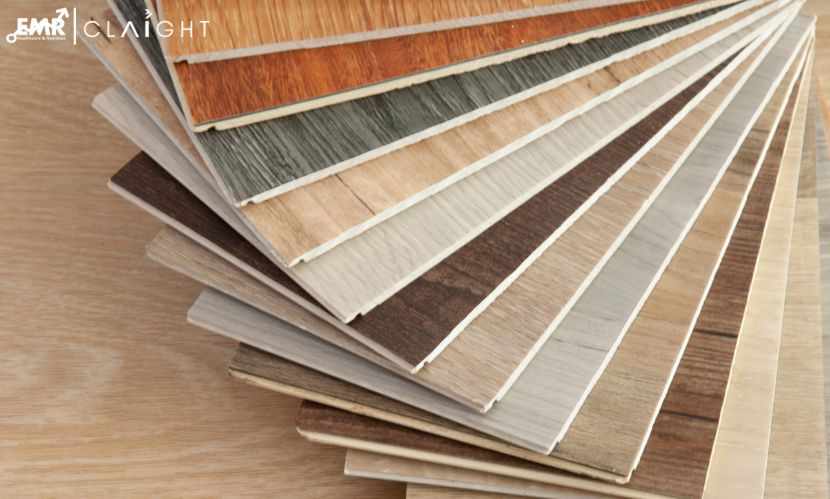
Plywood is a versatile engineered wood product widely used in construction, furniture manufacturing, and interior design due to its strength, durability, and aesthetic appeal. Made by layering thin sheets of wood veneer and bonding them with adhesive under heat and pressure, plywood offers excellent structural stability and resistance to warping. Establishing a plywood manufacturing plant requires strategic planning, an understanding of raw materials and production techniques, and adherence to quality standards to meet market demands and deliver a reliable product.
Overview of Plywood Production
The production of plywood involves a systematic process that ensures durability, uniformity, and a high-quality finish. It starts with procuring the right timber species, followed by peeling, drying, gluing, and pressing to create sheets of desired thickness and size. Modern plywood manufacturing also incorporates innovative techniques to enhance product features such as water resistance, fire retardancy, and anti-termite treatment. The demand for plywood spans various sectors, creating a stable market for manufacturers to thrive.
Get a Free Sample Report with Table of Contents@ https://www.expertmarketresearch.com/prefeasibility-reports/plywood-manufacturing-plant-project-report/requestsample
Key Components of a Plywood Manufacturing Plant
A plywood manufacturing facility requires essential machinery and infrastructure to streamline operations and ensure high-quality output. These components include:
Raw Material Storage:
Designated areas to store logs and timber under controlled conditions.
Measures to prevent moisture damage and pest infestation.
Log Peeling and Veneer Cutting Machines:
Machines to strip logs into thin layers or veneers.
Precision cutters to achieve uniform veneer thickness.
Drying Systems:
Dryers to remove excess moisture from veneers, ensuring optimal bonding.
Kiln drying systems for efficient moisture control.
Gluing and Assembly Units:
Equipment for applying adhesive evenly across veneers.
Facilities for stacking and aligning veneers in the desired grain orientation.
Pressing Machines:
Hydraulic or hot press machines to bond veneers under heat and pressure.
Systems to ensure uniform compression across the sheet.
Cutting and Finishing Units:
Machines for trimming plywood sheets to standard sizes.
Sanding units to smooth surfaces and prepare for lamination or painting.
Quality Control Laboratory:
Facilities to test the mechanical properties and durability of plywood.
Equipment to ensure compliance with industry standards.
Step-by-Step Guide to Plywood Manufacturing
Raw Material Procurement:
Source logs from sustainable forestry operations to ensure quality and availability.
Conduct quality checks to assess the suitability of timber species for manufacturing.
Log Preparation:
Debark and clean logs to prepare them for peeling.
Cut logs into manageable lengths for processing.
Veneer Production:
Use peeling machines to produce thin veneers from the logs.
Dry the veneers to achieve the desired moisture content.
Adhesive Application and Assembly:
Apply adhesive evenly to veneers using automated systems.
Assemble veneers in alternating grain orientations to enhance strength.
Pressing and Bonding:
Place assembled veneers into hydraulic presses for bonding under heat and pressure.
Allow sheets to cool and stabilise before further processing.
Cutting and Finishing:
Trim bonded plywood sheets to standard dimensions.
Sand surfaces to prepare for lamination or coating.
Quality Testing and Packaging:
Test finished plywood for properties such as strength, water resistance, and dimensional stability.
Package sheets securely for transport and storage.
Applications of Plywood
Plywood’s versatility makes it a preferred material across numerous industries. Key applications include:
Construction:
Used in roofing, flooring, and wall panelling due to its strength and durability.
Furniture Manufacturing:
A staple material for crafting tables, cabinets, beds, and other furniture items.
Interior Design:
Popular for decorative purposes, including wall cladding, partitions, and false ceilings.
Industrial Use:
Employed in packaging, transportation, and manufacturing pallets.
Marine Applications:
Special grades of plywood are used in shipbuilding and for outdoor structures.
Safety and Environmental Considerations
Manufacturing plywood involves the use of adhesives and machinery that require careful handling to ensure worker safety and environmental protection. Key considerations include:
Worker Safety:
Provide training on safe machinery operation and handling of chemicals.
Equip workers with protective gear such as gloves, masks, and eyewear.
Waste Management:
Recycle wood waste and sawdust to minimise environmental impact.
Implement systems for proper disposal of adhesive and chemical residues.
Emission Control:
Install filtration systems to reduce emissions from adhesives and other processes.
Monitor air quality in and around the plant regularly.
Sustainable Practices:
Use timber from certified sustainable sources.
Incorporate eco-friendly adhesives and treatments.
Operational Challenges
Setting up and managing a plywood manufacturing plant comes with challenges that require strategic planning and management. These include:
Raw Material Availability:
Ensuring consistent supply of high-quality timber.
Mitigating the impact of deforestation and seasonal availability.
Technological Upgrades:
Keeping up with advancements in machinery to enhance production efficiency.
Investing in automation for quality improvement and cost reduction.
Market Competition:
Competing with established brands and imported plywood products.
Differentiating through innovation and superior quality.
Regulatory Compliance:
Adhering to environmental and safety regulations.
Conducting regular audits to maintain certifications.
Emerging Trends in Plywood Manufacturing
The plywood industry is evolving with technological advancements and changing consumer preferences. Key trends include:
Sustainable Production:
Increased focus on using eco-friendly materials and processes.
Adoption of energy-efficient machinery to reduce carbon footprints.
Innovative Products:
Development of specialised plywood variants such as fire-resistant and waterproof grades.
Introduction of decorative laminates and textured finishes.
Automation and Digitalisation:
Integration of automated systems for precision and efficiency.
Use of data analytics for process optimisation and quality control.
Global Expansion:
Growing export opportunities in emerging markets.
Collaborations with international distributors to expand reach.
Economic and Social Impact
Establishing a plywood manufacturing plant contributes significantly to economic growth and community development. Benefits include:
Job Creation:
Provides employment opportunities for skilled and unskilled workers.
Support for Forestry:
Encourages sustainable forestry practices and timber cultivation.
Boost to Local Economy:
Stimulates regional development through infrastructure and resource utilisation.
Export Opportunities:
Enhances the country’s presence in global markets through quality plywood products.
By focusing on innovation, sustainability, and operational excellence, plywood manufacturers can cater to diverse market demands and drive long-term growth.
Write a comment ...